Despite the best planning, every manufacturing company faces minor or major disruptions and crises in their day-to-day operations. Ideally, every required resource should be available at the right time, in the right quantity, and in the right place. However, shortages of resources such as production materials, auxiliary materials, tools, equipment, or workforce can unexpectedly occur. For example, a machine breaks down, delivered materials turn out to be of poor quality, or a team is hit by an outbreak of illness.
The Issue Management Dashboard is designed to efficiently and optimally address such situations. While traditional paper-based or Excel-based processes tend to create new delays when dealing with existing ones, the Issue Management Dashboard helps to quickly and smoothly get production back on track. Additionally, by analyzing the encountered problems, their root causes, and implemented solutions, the gathered information can be used to prevent similar issues in the future.
In production, it is not possible to completely avoid issues, but a plan must also be in place to address them
An issue signifies a shortage of some input in production, whether it be materials, auxiliary materials, tools, equipment, or workforce. Due to this shortage, production either stops or gets delayed. Therefore, continuous re-planning and optimization are necessary in production to maximize output with limited resources.
Certainly, the Issue Management Dashboard does not replace planning. As they say, if you fail to plan, you plan to fail. Issue management serves as a plan B when the initial plan fails for any reason.
When there is no clear procedure for issue resolution, and information is only passed on through paper or Excel spreadsheets, the resolution process tends to take much more time than necessary. Process optimization is not possible without clear priorities and accountability.
Why does issue resolution usually get delayed?
- Lack of clear accountability and action plan – the issue remains in limbo, and relevant individuals may not even be aware of its occurrence; management lacks an overview of the incidents.
- Lack of information flow – necessary information remains in someone's mind or on paper, which can cause a complete halt in issue resolution if that person, for example, falls ill.
- Delays between different departments – in case of an issue, regular procedures cannot be followed, and departments need to collaborate swiftly.
- Delayed workflow hampers subsequent tasks – for instance, replacement parts cannot be received in the warehouse on a priority basis, and sometimes, they are not even aware that it needs to be done.
In summary, issue resolution takes too long, and there is no systematic way to prevent similar issues from happening. Often, there is an attempt to conceal the problem, exploiting planned time buffers in the process. However, concealing the problem only causes more delays and increases the chances of repeating the issue.
The Issue Management Dashboard provides a centralized platform where all issues become visible
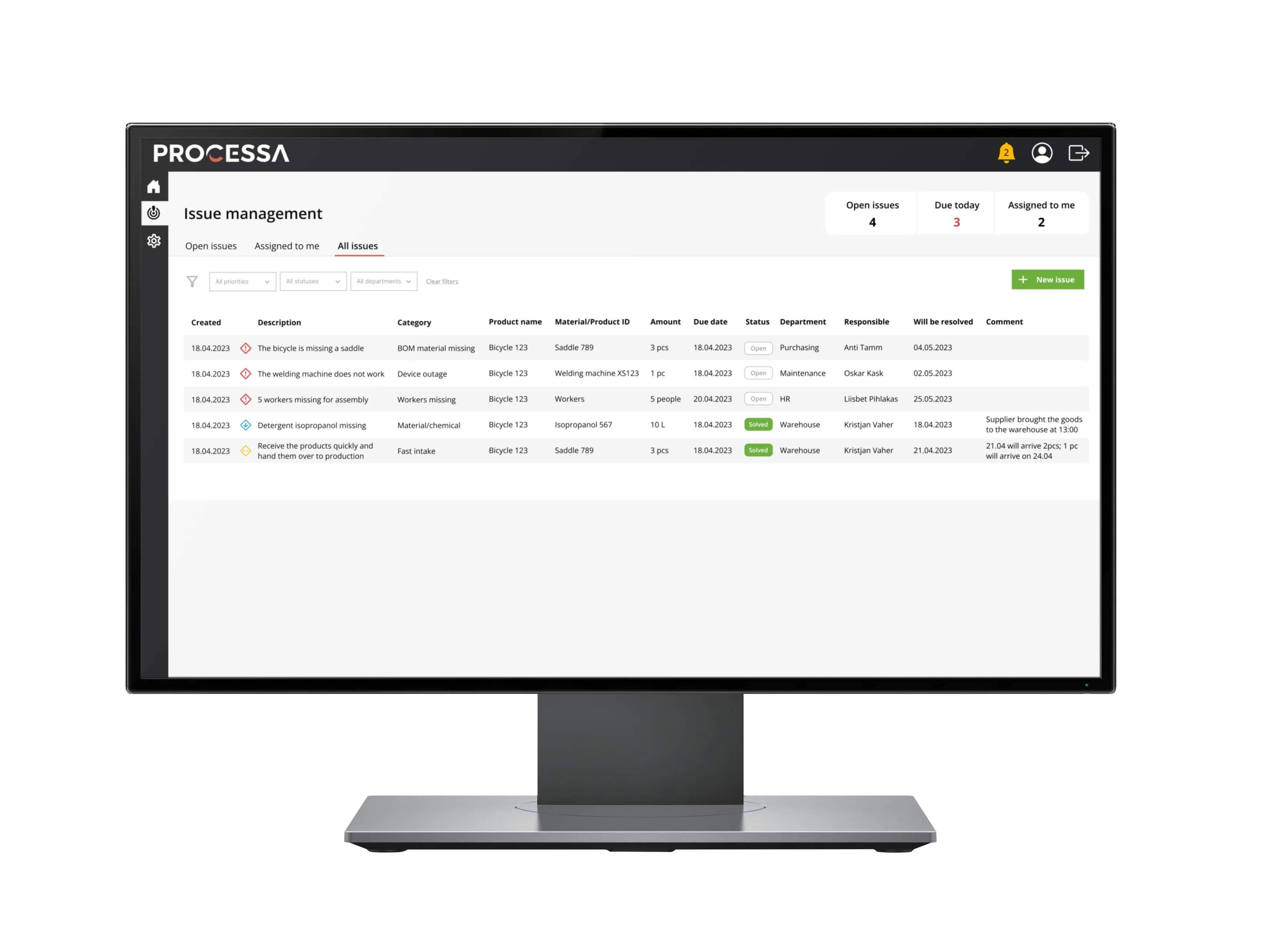
It becomes easier to set and adjust priorities based on the urgency and impact of the issues. The dashboard offers a clear workflow for issue resolution, specifying the responsible person, objective, and deadline. This ensures that issues are not lost or forgotten and are actively worked on until resolved.
How does an issue management dashboard contribute to finding solutions?
An issue management dashboard makes all the problems within the company clearly visible. This creates a clear plan and responsibility for resolving the issues.
- Making issues visible – Information about the encountered problems is not confined to employees' minds, email exchanges, or spreadsheets. All relevant employees, departments, and management have a real-time overview of ongoing incidents and their status.
- Creating ownership and accountability – Once an issue is logged on the issue management dashboard, a specific person is responsible for resolving it at any given time. Even if the solution involves multiple departments, the responsibility lies with an individual from each department.
- Replaceable accountability – If the accountable person is absent due to illness or any other reason, the status of the issues is consistently recorded, and the replacement receives precise information, ensuring the process continues smoothly.
- Establishing a defined workflow with goals and deadlines – Everyone knows who needs to do what and by when (who, what, when) to resolve the issue in the best possible way.
- Prioritizing issue resolution over new tasks – For example, materials or equipment required for resolving the issue are expedited rather than waiting in the general receiving queue.
- Resolving issues quickly and effectively – Ultimately, the goal is to reach a solution as promptly and efficiently as possible, considering the conditions and constraints of the issue.
- Generating a systematic log and overview of issues for process improvement – Valuable information accumulates from the issues and their resolutions, which can be used to avoid similar problems in the future or resolve them more rapidly. While it's not possible to completely eliminate issues, continuous improvement must take place within the company. It cannot happen without specific information – what you can measure, you can improve.