The principle of production planning known as Plan For Every Part (PFEP), which can roughly be translated as "planning for every part", is not a new concept, but is still relatively unknown among Estonian manufacturers. PFEP is particularly important when dealing with a product that is still under development and consists of a large number of different components (a complex Bill of Materials or BOM).
PFEP improves collaboration between teams, reduces waste, increases supply chain flexibility, and helps the company stay competitive in every way. In this post, we introduce what PFEP is, what its goals are, and how to get started with it.
What is PFEP, or Plan For Every Part?
PFEP is a systematic, centralized, and accessible application used in project management and implementation of a product in development. It can also be used to manage changes related to components in production and their suppliers.
For each component, PFEP can map the following information:
- Component number, manufacturer, description, dimensions, etc.;
- Where and how it is supplied;
- How it should be packaged and stored;
- When it is used and how often, etc.
Data is the lifeblood of almost every company, therefore organizing and centralizing data is the foundation of optimizing a company's operations. Every manufacturer's goal should be to understand and maximize the use of their data. As the name suggests, developing PFEP optimizes how the company develops and uses each necessary component for production, and makes component developments and changes visible to different stakeholders.
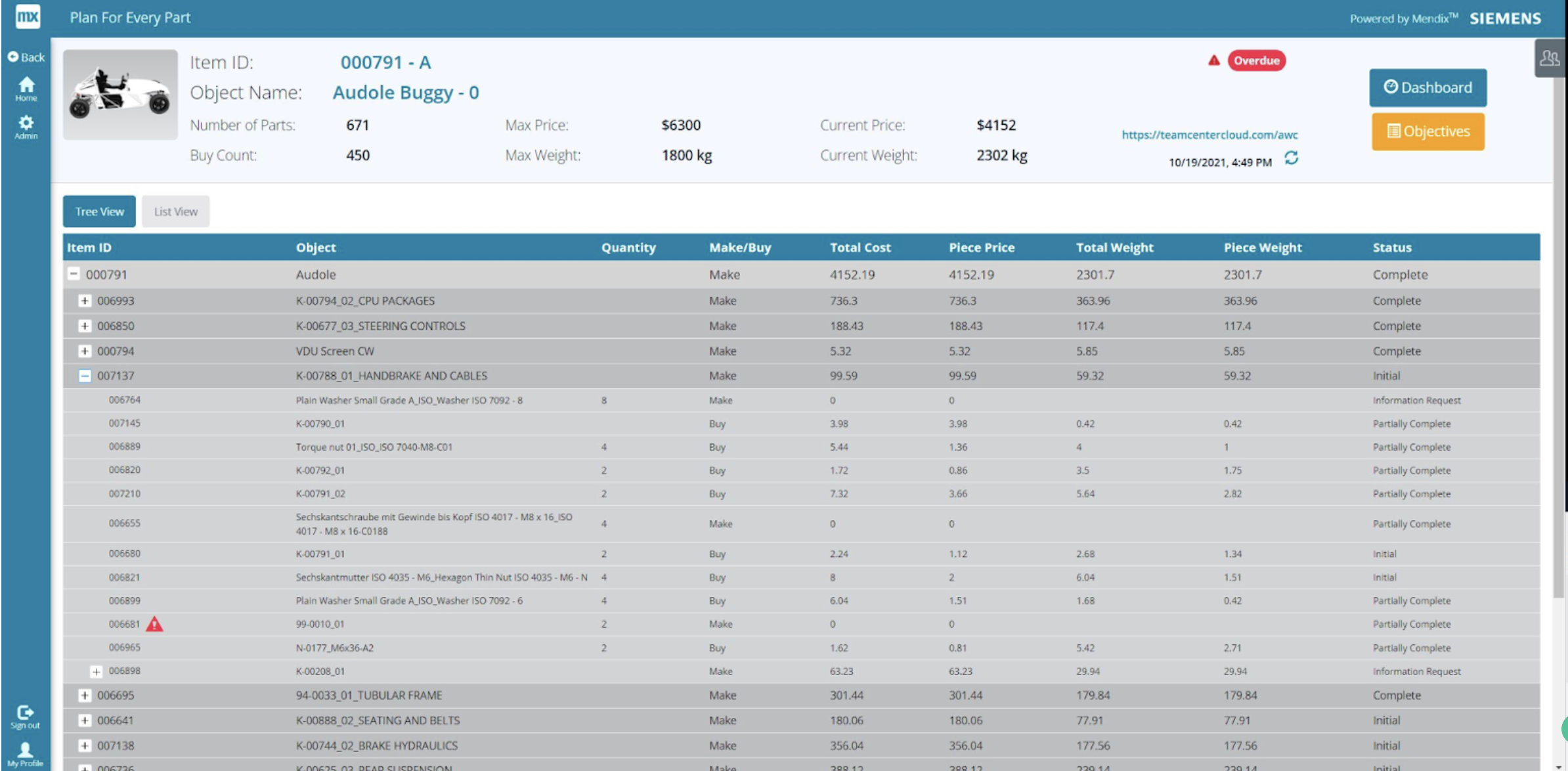
This gives PFEP project managers a 360-degree view of the status of components and the project. Usually, this information remains hidden because it is located in different systems that are not accessible at the right time or place. Manufacturing companies can no longer afford to store such fragmented or encapsulated data. Supply chain flexibility can no longer be considered a competitive advantage; it is essential for today's businesses to stay competitive.
The central goal of PFEP is to improve collaboration between teams, reduce waste, increase supply chain flexibility, and help the company stay competitive in every way. The creation of PFEP is the foundation for product development and cross-functional collaboration, and process optimization. When combined with MRP, for example, it provides necessary information in real-time and in a simplified manner to all teams involved in the different stages of the product.
Supply chain instability is here to stay
Given the increasing complexity of supply chains, introducing new products and optimizing supply chains may seem like an impossible task. Supply chain managers are already juggling missing and excess inventory on a daily basis while ensuring timely completion and delivery of products.
However, recent events have clearly shown the opposite – supply chain flexibility is no longer a luxury but a necessity. Supply chain problems related to the pandemic have simply exposed that long-term globalization and the resulting scattering of supply chain components around the world have led to complex systems that cannot be quickly redesigned. Smart procurement and planning help mitigate these risks, and modern technologies provide essential visibility and flexibility.
Developing a PFEP is the main way companies can increase supply chain resilience and prepare for both expected and unexpected changes. When developing and implementing a PFEP, emphasis should be placed on ensuring that people working with the supply chain have full access to the PFEP system. This way, they can provide valuable input to the product development process and help ensure a cost-effective supply chain for the company.
Why is creating a PFEP beneficial?
Well-established and managed PFEP helps:
- Improve collaboration between teams,
- Reduce waste,
- Increase supply chain readiness and thus flexibility,
- Produce more efficiently,
- Save money on product development and implementation.
PFEP goes hand in hand with so-called cost-effective or lean manufacturing, which focuses not only on value-creating activities but also on reducing value-wasting activities. For example, when optimizing production or applying lean principles, the focus is often on labor. However, depending on the product being produced, the cost of materials alone can account for up to 50-80% of the product's cost.
About 70-80% of the final cost of the product comes from the design process and the materials used. Simply involving the procurement department early in the product design process can reduce production costs by up to 20%. Even a small change in the BOM means managing changes and going through various approval rounds. In addition, manufacturers often find that when implementing PFEP, they actually use a relatively small part of their inventory list to produce most of their products, reducing inventory levels by about 50%.
An overview of the status of activities related to the new product.

How to get started with PFEP?
The level of detail required to create a PFEP-like master plan can be daunting, especially for companies with a wide range of products. However, most manufacturers already have the data they need to create these plans, but it is stored only in people's memories or spreadsheets. These are disconnected and not easily accessible, requiring a lot of manual work when changes need to be made. Now is the time to consolidate, sort, and implement them for the benefit of the company.
Each company's needs and processes are different, so it is impossible to provide a specific PFEP template. However, it is worth keeping in mind some simple principles when creating a personalized PFEP for the company.
Real-time reporting
Automating reporting and bringing it into real-time makes passive data actively usable information. The ability to use and analyze different PFEP data in real-time provides various teams with the right information to make better decisions. It also ensures data updates and relevance.
Consolidate existing data
Create a database of all components used in production, including alternatives sourced from the market. Note that the data should be reduced to the smallest possible unit, such as entering separate height, width, and depth instead of the measurements of a part in one cell. And start with simplicity, complexity can always be added.
Take it as a journey, not a destination
Like the lean principle, PFEP is a journey, not a destination - it must support flexibility and reduce the team's workload to ensure continuous successful production. Creating such an implementation can take a long time but can bring drastic positive changes to product development, production implementation, and work organization. And that time will pass anyway.
Processa Technologies is a Siemens Mendix partner in the Baltics. Mendix is a low-code platform that allows 7-10x faster software development and is ideal for digitalizing production processes and creating integrations.