In the competitive landscape of the manufacturing industry, companies are continuously seeking innovative solutions to enhance their operational efficiency and throughput. This case study explores how a Radius Machining achieved a remarkable 38.5% increase in internal locistics throughput by integrating Processa SmartPicker, the Monitor ERP G5 add-on into their existing systems.
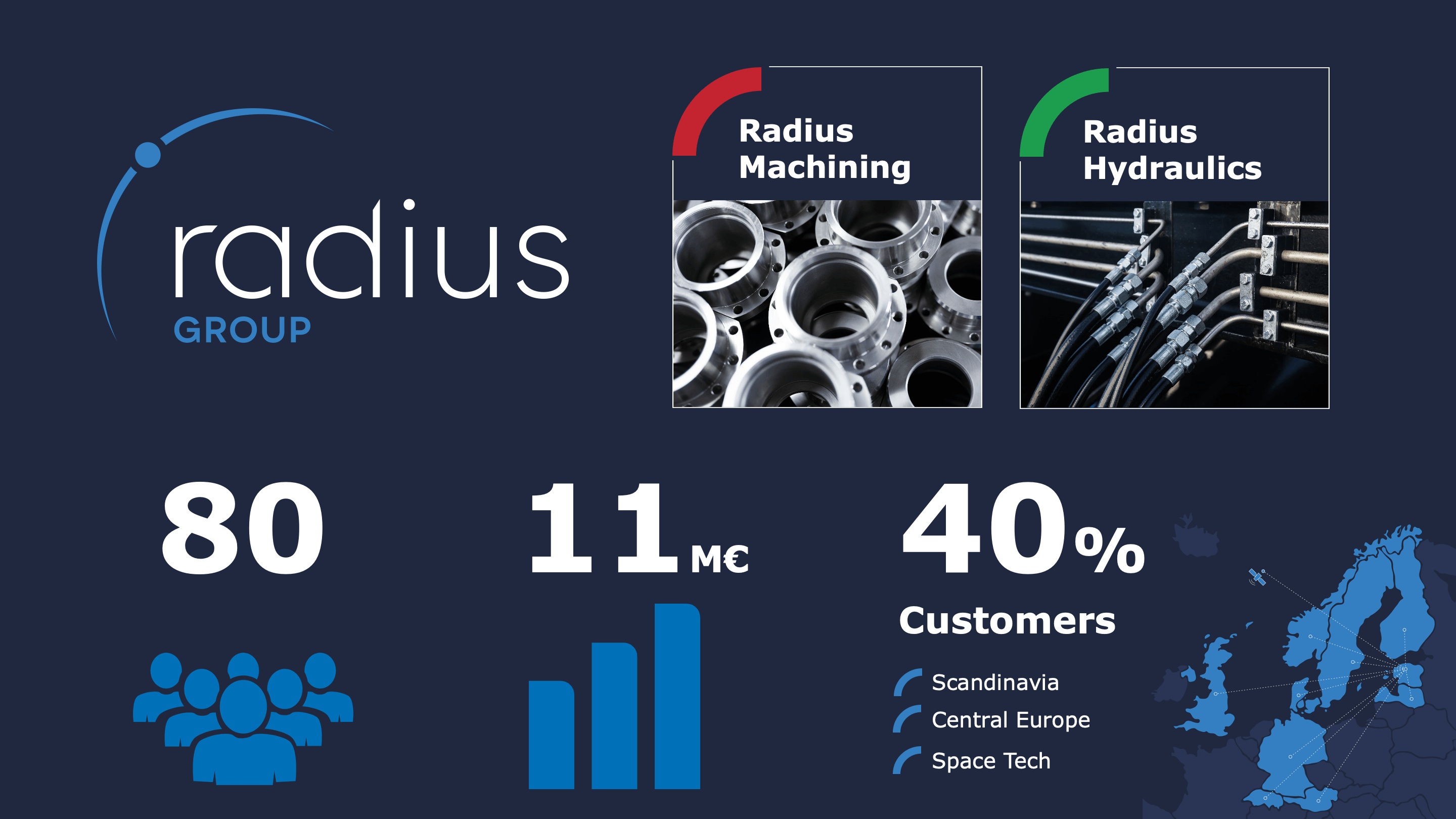
Radius is a contract manufacturing company with two business units providing CNC machining services & hydraulic assemblies for the OEM sector.
- Export markets: Scandinavia, Central Europe, Aerospace
- Exports: 40%
- Challenge: Managing logistics and reducing paperwork in a complex, dynamic manufacturing environment.
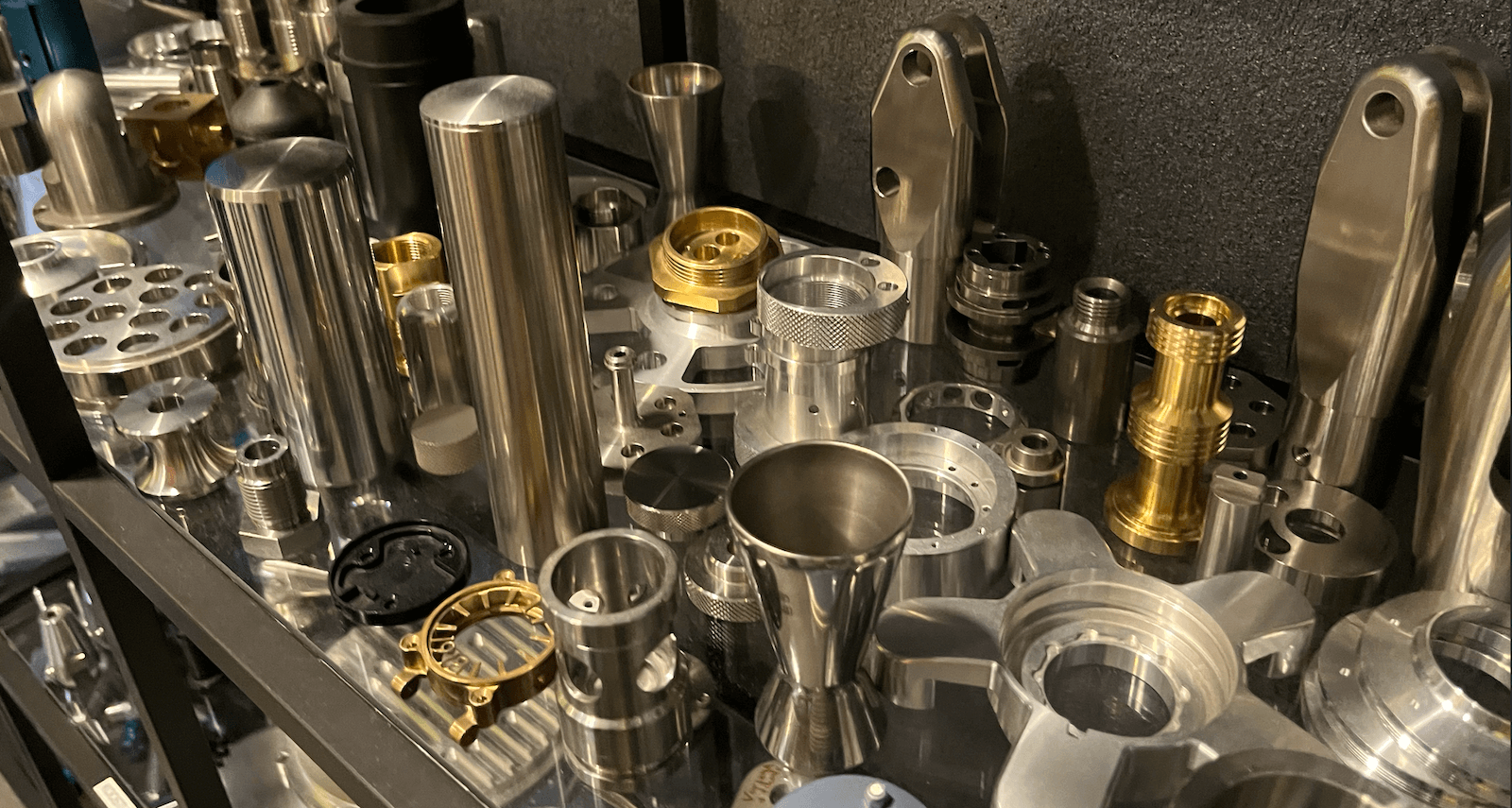
Challenge
The company faced significant operational challenges that hindered its daily activities and overall productivity:
- Difficulty in synchronizing paper-based information to formulate dispatch notes, affecting throughput.
- Managing changes in customer requirements was cumbersome.
- Assessing workload and planning ahead was nearly impossible due to the reliance on extensive printing and manual processes, limited access to the ERP system, and the absence of system-integrated packing instructions.
Solution
The decision to adopt Processa SmartPicker, the Monitor ERP G5 add-on, was driven by the need for a responsive, easy-to-integrate solution that could address the specific challenges faced by the company.
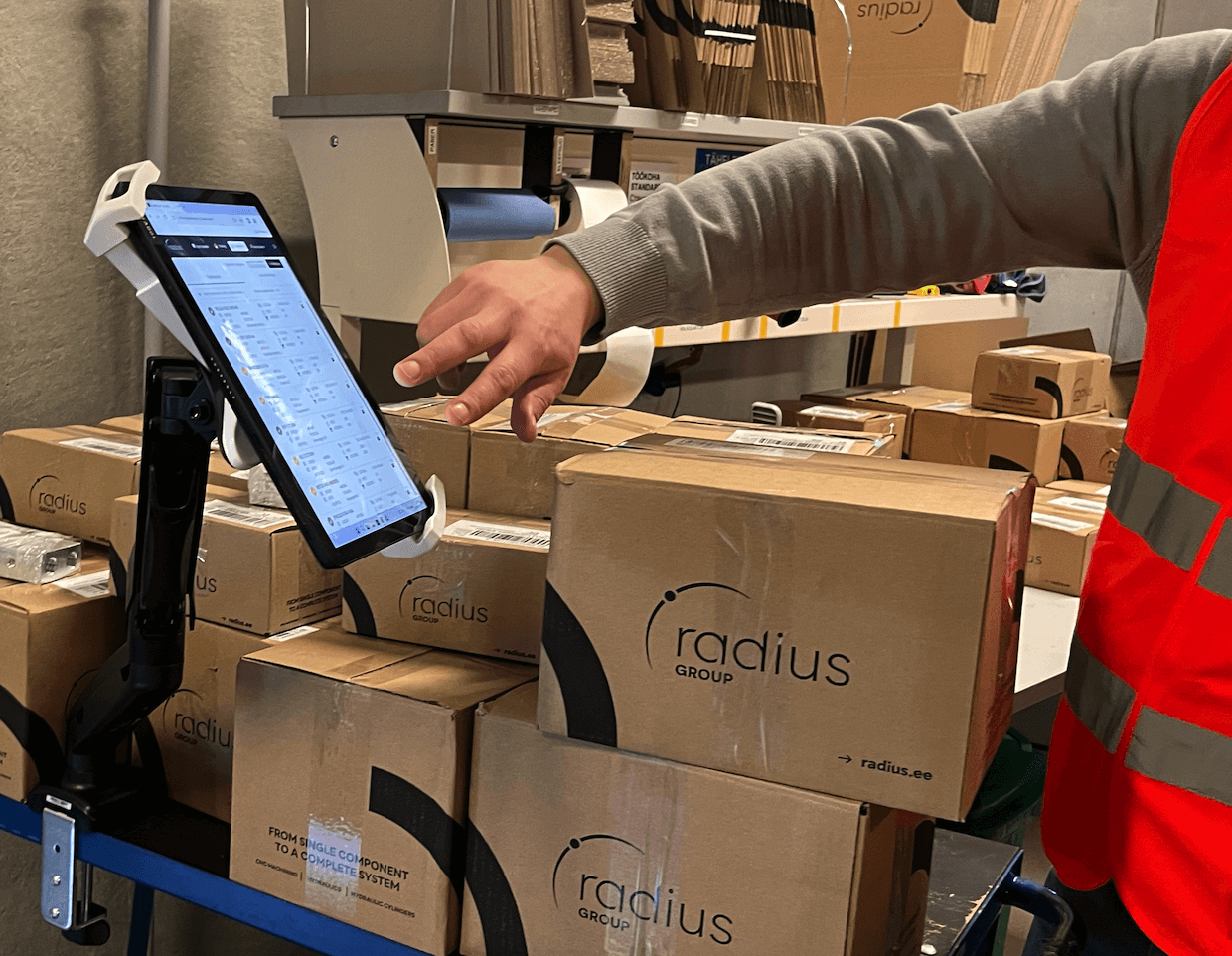
Key aspects of the solution included:
- Low-Code Platform Integration: Utilizing Siemens Mendix certified development partner, Processa Technologies, for rapid and flexible software development.
- Process Automation: Focusing on internallogistics automation to create a competitive advantage.
- Monitor ERP G5 Integration: Direct integration with the ERP system for real-time data on production orders, operations, inventory statuses, and updates.
- Mobile and Responsive Application: Implementation of tablet devices for warehouse staff to manage lists effectively, supporting quick iterations and changes.
Results
Increase in internal logistics throughput by 38.5%, without the need for additional human resources.
The implementation of Processa SmartPicker yielded impressive outcomes, significantly transforming the company's operational efficiency:
- Increased Throughput: A substantial increase in throughput by 38.5%, without the need for additional human resources.
- Reduced Paperwork: Elimination of excessive printing, leading to a daily saving of 1-2 hours per employee.
- Improved Accessibility and Adherence to Instructions: Enhanced availability of guidelines and adherence to them, thanks to digitalization.
- Faster and Higher-Quality Information Exchange: Streamlined communication and information exchange processes across the company, mainly impacting the internal logistics team.
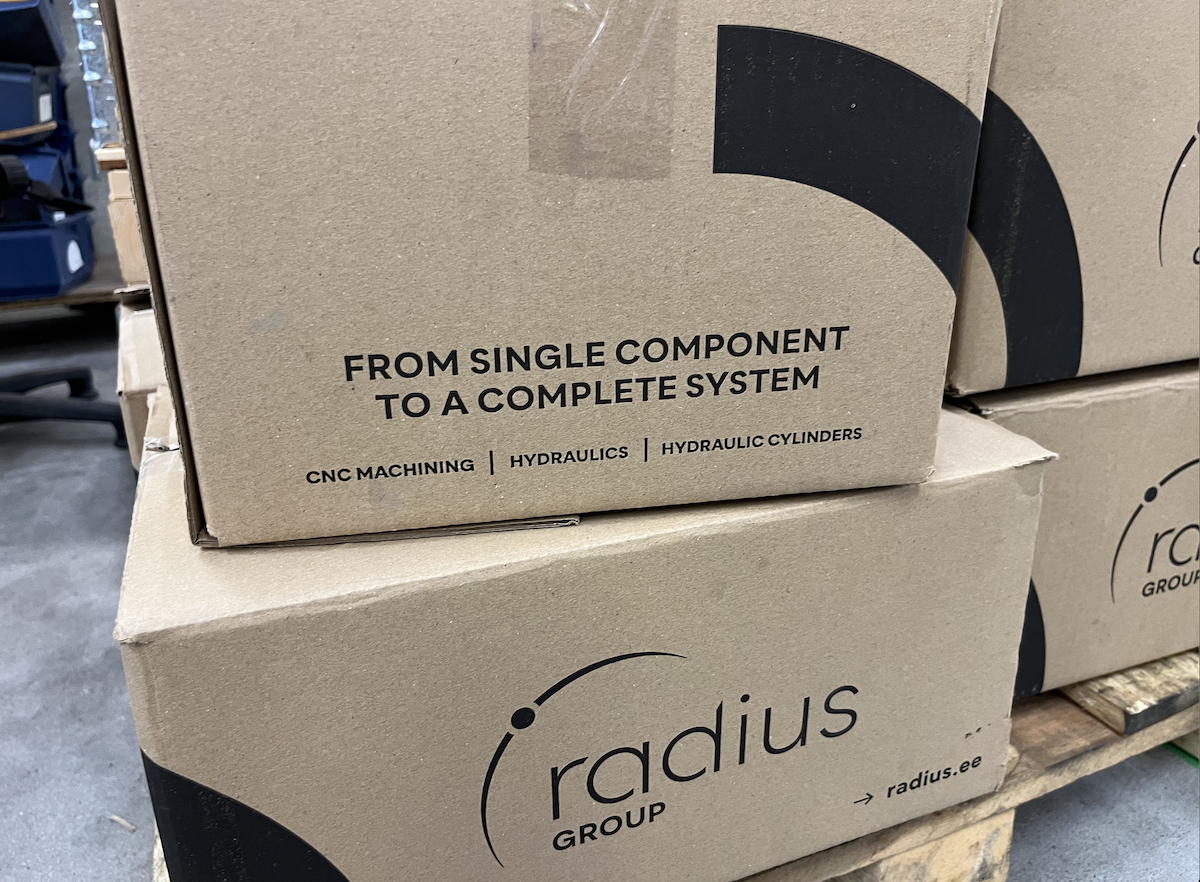
Lessons Learned
The journey of integrating the Monitor ERP G5 add-on provided valuable insights:
- Engage stakeholders and specialists early in the process.
- Allocate sufficient time for testing and iteration.
- Consider the technical aspects carefully, such as device selection and hardware integrations (e.g. printing).
Future Outlook
Motivated by the triumphant integration of the Monitor ERP G5 add-on, Processa SmartPicker, the new Instrument Registry was rapidly deployed. The registry facilitates the check-out and check-in of tools, allowing for meticulous monitoring of their usage. This usage-based approach to calibration and verification of tools leads to substantial cost reductions, saving tens of thousands of euros annually. Looking ahead, we aim to integrate work time measurement with payroll systems and enhance data visualization, thereby empowering strategic decision-making in the near future.
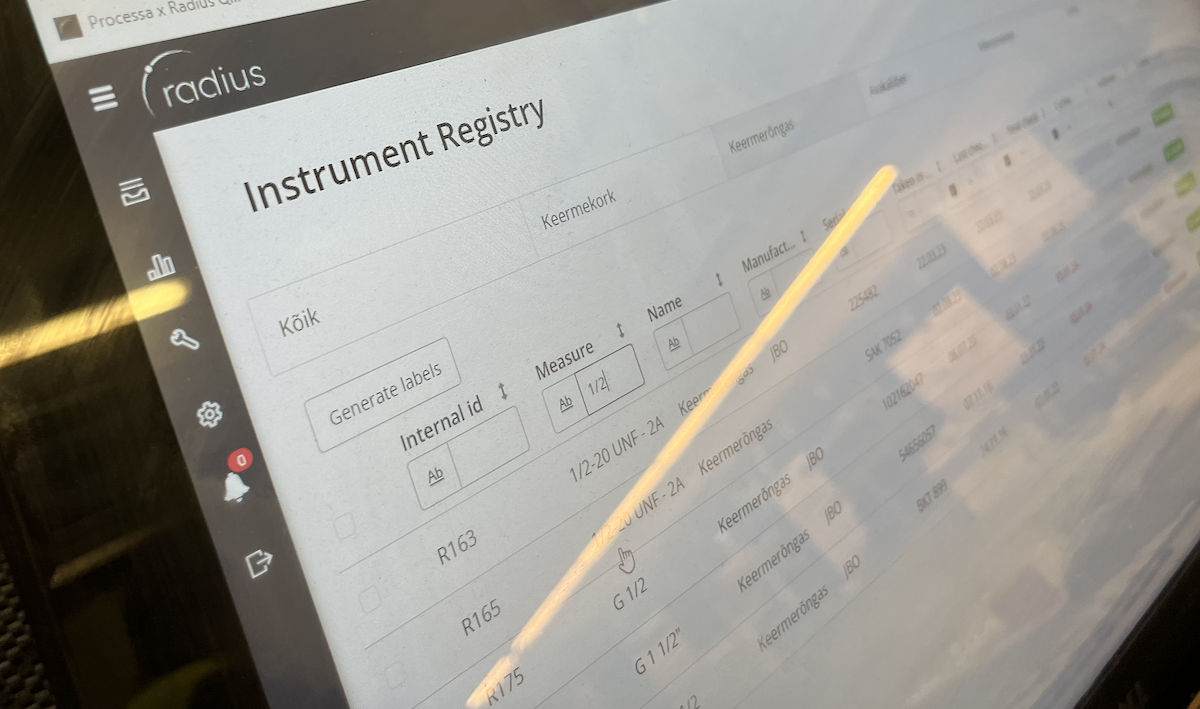
Conclusion
The case of Radius Machining internal logistics improvement demonstrates the transformative potential of Processa SmartPicker in enhancing productivity, and enabling significant throughput increases.
By embracing digital solutions and process automation, companies can achieve competitive advantages in the rapidly evolving manufacturing sector.